Na co zwrócić uwagę podczas relokacji maszyn?
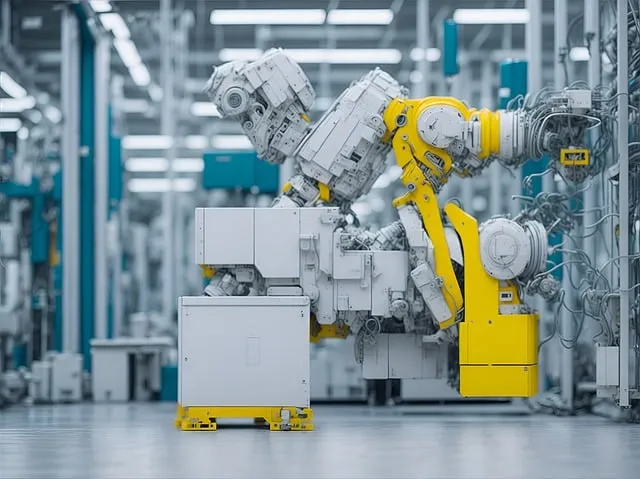
Relokacja maszyn to proces, który wymaga precyzji, doświadczenia i dokładnego planowania. Niezależnie od tego, czy maszyny są przenoszone w obrębie jednego zakładu, czy na duże odległości, każda relokacja niesie ze sobą wyzwania, które mogą wpłynąć na ciągłość produkcji, koszty oraz efektywność urządzeń po ich ponownym uruchomieniu. Dlatego ważne jest zwrócenie uwagi na szereg aspektów, które mogą przesądzić o sukcesie całego przedsięwzięcia.
Przyjrzymy się czynnikom, które należy wziąć pod uwagę podczas planowania i realizacji relokacji maszyn.
Ostrożny i przemyślany demontaż maszyn
Demontaż maszyn to etap relokacji, który wymaga niezwykłej precyzji i uwagi. Niewłaściwe rozłożenie urządzeń może prowadzić do uszkodzeń ich komponentów, co z kolei generuje dodatkowe koszty i wydłuża czas realizacji całego procesu. Dlatego demontaż powinien być dokładnie przemyślany i zaplanowany, z uwzględnieniem dokumentacji technicznej oraz specyfikacji maszyn. Istotne jest, aby każdy element był odpowiednio oznakowany i zabezpieczony, co ułatwi ponowny montaż i minimalizuje ryzyko błędów.
Kolejnym ważnym aspektem jest użycie odpowiednich narzędzi i technologii, które pozwalają na bezpieczne i skuteczne rozłożenie nawet najbardziej zaawansowanych urządzeń. W przypadku maszyn o dużych gabarytach lub wysokim poziomie złożoności konieczne jest zastosowanie specjalistycznego sprzętu, takiego jak dźwigi czy podnośniki hydrauliczne. Demontaż powinien być również prowadzony przez doświadczony zespół techników, który potrafi przewidzieć potencjalne trudności i zadbać o bezpieczeństwo zarówno maszyn, jak i pracowników.
Wcześniej zaplanowany transport urządzeń
Transport urządzeń to jeden z najbardziej wymagających etapów relokacji maszyn, dlatego wcześniejsze zaplanowanie wszystkich szczegółów jest ważne dla jego powodzenia. Proces ten wymaga nie tylko organizacji odpowiedniego środka transportu, ale również uwzględnienia specyficznych wymagań przewożonych maszyn, takich jak ich wymiary, waga czy delikatność komponentów. Przed załadunkiem należy zadbać o właściwe zabezpieczenie urządzeń, które chroni je przed uszkodzeniami mechanicznymi, wibracjami czy niekorzystnymi warunkami atmosferycznymi.
Ważnym elementem planowania jest również analiza trasy, uwzględniająca ewentualne ograniczenia drogowe, takie jak mosty, tunele czy przepisy dotyczące transportu wielkogabarytowego. W przypadku transportu międzynarodowego należy dodatkowo wziąć pod uwagę kwestie celne i regulacje obowiązujące w kraju docelowym. Wcześniejsze opracowanie harmonogramu i dokładne przygotowanie transportu pozwala uniknąć opóźnień i problemów logistycznych, zapewniając płynny przebieg relokacji. Więcej o tym aspekcie dowiesz się na https://pserwis.pl/oferta/transfery-linii-produkcyjnych-i-urzadzen-przemyslowych
Testy maszyn po ich relokacji
Testy maszyn po relokacji są niezbędnym etapem, który gwarantuje, że urządzenia działają prawidłowo i są gotowe do wznowienia produkcji. Po montażu wszystkie maszyny powinny zostać dokładnie sprawdzone pod kątem poprawności podłączeń, funkcjonalności oraz zgodności z dokumentacją techniczną. Testy obejmują zarówno podstawowe uruchomienie, jak i bardziej zaawansowane próby w warunkach obciążenia produkcyjnego, które pozwalają ocenić, czy urządzenia pracują z odpowiednią wydajnością i precyzją.
Warto również przeprowadzić kalibrację maszyn, aby dostosować ich parametry do specyfiki nowej lokalizacji lub zmienionych procesów produkcyjnych. Podczas testów technicy mogą wychwycić potencjalne problemy, takie jak niewielkie błędy montażowe czy uszkodzenia komponentów, i natychmiast je skorygować, zanim urządzenia zostaną w pełni wdrożone do pracy. Dzięki rzetelnym testom firma zyskuje pewność, że relokowane maszyny są bezpieczne, wydajne i gotowe do długotrwałego użytkowania, co minimalizuje ryzyko kosztownych awarii czy przestojów.
Autor: Materiał partnera